A Comparison Of ISO 9001 And Quality Management System
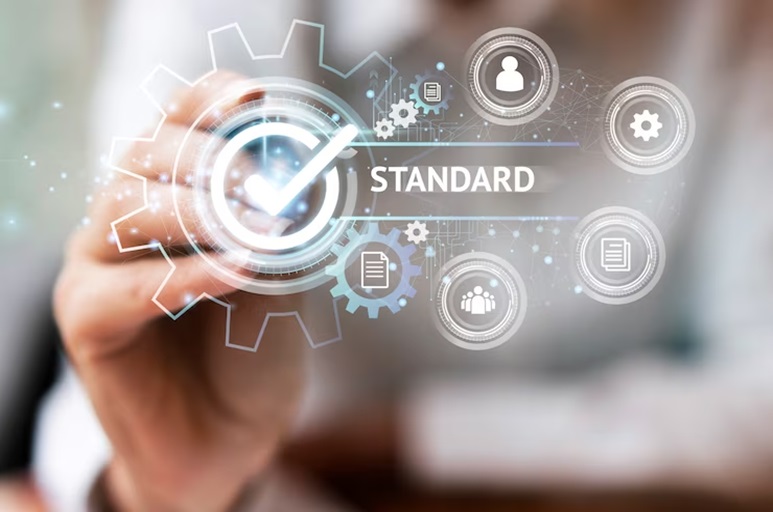
Process standardisation is a prevalent practice for businesses. The best practices in a certain field are extremely condensed and established by specialists aware of the requirements in that field. A standard might specify how to design a product, control a procedure, or provide a service.
Industry standards have historically been created to help firms conform to external norms and give their clients and suppliers a clear grasp of their procedures.
Although several other organisations have developed standard systems, the ISO is the most widely used. This is so that businesses may maximise the effectiveness of their quality management system. Companies that want to ensure compliance, quality standards and customer satisfaction will get ISO certification in Qatar.
However, many businesses view both phrases as interchangeable. You may learn about the similarities and differences between ISO 9001 and quality management systems here.
ISO 9001:2015
The requirements for a quality management system (QMS) are outlined in ISO 9001, an international standard. It shows that a business can continuously offer products and services that satisfy customers’ needs and legal requirements. This is the most widely used and the only ISO 9000 standard that may be certified.
The ISO 9001 international standard was established in 1987 and created by 160 national standard-setting organisations from over 160 nations. The most recent iteration of ISO 9001 was published in September 2015.
Regarding ISO 9001:2015, there are no restrictions on size or industry. Over a million enterprises have adopted the ISO 9001 standard in more than 160 nations. All sizes and types of enterprises benefit from ISO 9001:
- Process simplification and standardisation
- Process improvement will boost effectiveness.
- Constantly get better
Organisations may constantly serve their customers with high-quality goods and services thanks to ISO 9001, which raises customer, employee, and management satisfaction.
Organisations utilise ISO 9001 because it outlines the conditions necessary for a successful quality management system, enabling them to:
- Create a quality control system.
- satisfy management, staff, and customers
- constantly enhance their procedures
- Cut expenses
You get a framework with ISO 9001 to establish and meet quality goals on schedule. It outlines every best practice that a company may use to create a culture of excellence and ongoing progress. Additionally, it aids in the effective and efficient management of change, ensuring that change is no longer viewed as a challenge in the company environment.
Let’s delve deeper to comprehend the quality management system and the related processes as ISO outlines the QMS standards. Understanding the procedures will make it easier than ever for you to put best practices into practice.
Establishing the Quality Management System
Quality Management Systems describe a company’s plans to provide high-quality goods and services while adhering to legal obligations. By implementing numerous quality management activities, a unified quality management system can span the complete lifecycle of a good or service.
- Planning: ensuring that all law and regulation requirements and client demands are met.
- Establishing procedures to ensure consistently high product quality is known as quality control.
- Ensure that your product fulfils your customers’ expectations through quality assurance.
- Enhancement: Making adjustments to your procedures and evaluating your results to make sure your standards are met and your clients are happy
- A QMS must be documented, but it must not be confused with the management system. Keeping records of your policies and developing process maps throughout the planning stage will help you train staff and ensure they understand what is required during Quality Control. The document aids in efforts for both quality assurance and enhancement because it serves as a standard for evaluating and judging a product’s or service’s level of quality.
In a QMS, risks are considered, whether or not they impact the quality of goods or services. Failures in the quality of the goods or services are also included here, as are failures to recognise client needs, adhere to legal obligations, and preserve customer security. A QMS will address and manage these issues, even when partnerships or suppliers may be to blame for these failures.
How Are ISO 9001 and QMS Related?
Our talk above should have clarified that QMS and ISO 9001 are closely related. You must create an ISO 9001-compliant quality management system to offer excellent products while maintaining compliance.
To conduct business, a company does not need to be certified to ISO 9001:2015. It has a bigger effect when they wish to offer their goods and services internationally.
Therefore, you can build quality management systems that align with best practices if you want to begin your journey toward quality without getting certified.
You may submit applications for ISO 9001 certification after you are certain about the quality culture in your business and wish to expand it internationally.
Shared Objectives for ISO 9001 and QMS
While ISO 9001 and QMS are two distinct but related concepts, they have certain similar objectives, such as:
- Ensuring the offered goods and services are high-quality, secure, and dependable.
- Creating a productive workplace.
- Ensuring staff and consumer happiness.
- Creating effective procedures for producing high-quality results.
- Increasing market share and brand credibility.
As was already said, QMS and ISO 9001 have some similar objectives. With the appropriate methodology, tools, and approach, you can do them. You could lose out on several commercial prospects if you don’t have the right team to assist you with the certification and auditing process.
Cooperating with an ISO certification consultancy to manage end-to-end quality procedures and standardise best practices workflows to leverage increased performance, scalability, adaptability, and security would be advisable.
A quality management system (QMS) is a framework that connects all of your quality operations to deliver high-quality products, whereas ISO 9001 represents the set of QMS requirements. You can satisfy compliance and all of your quality goals with its assistance.