Rotary Vane vs. Rotary Screw Compressors: What’s the Difference?
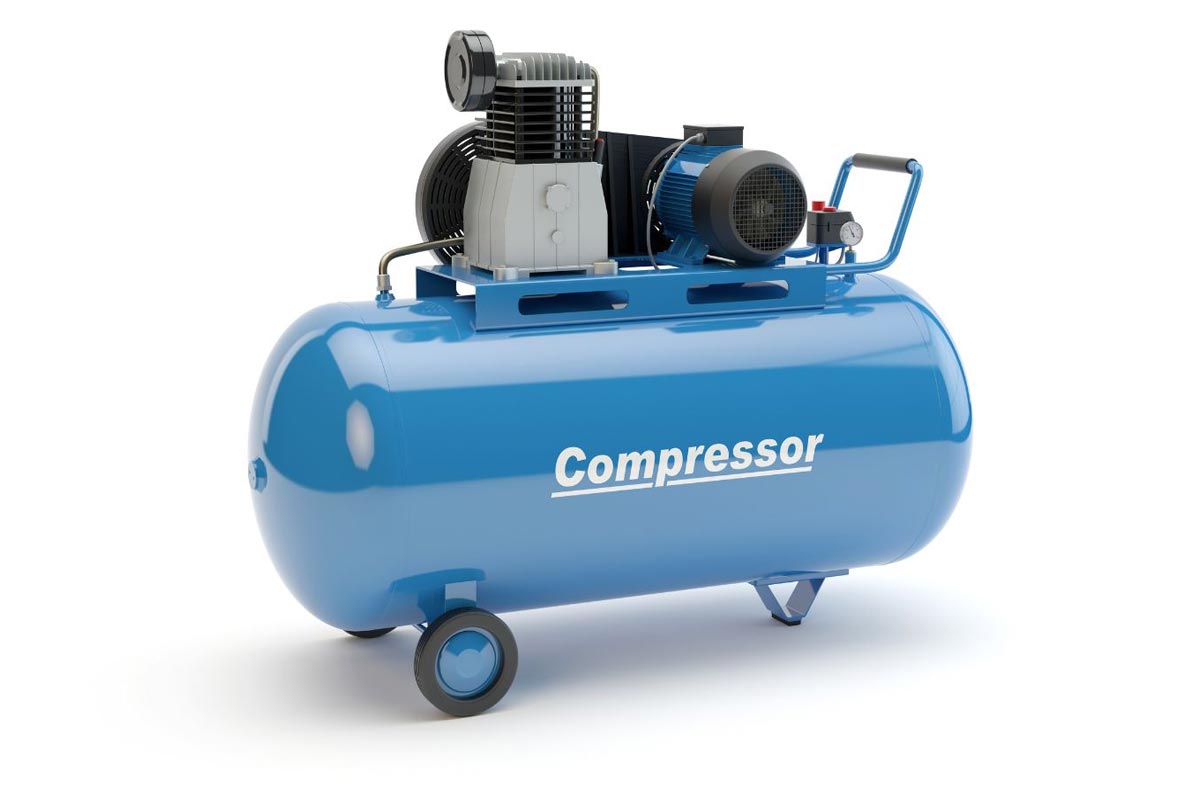
Since air is a safe, versatile, clean, and comfortable resource, air compressors have been used in the industry for more than 100 years. In many of the applications they support, these devices have become very reliable for almost versatile equipment. Air compressors are designed in a range of styles and sizes.
These two compressors are made for continuous operation. Therefore, they are ideal for a personal project, workshop tasks, challenging industrial or manufacturing environments that require large quantities of compressed air and long service life.
Rotary screw compressors operate on the theory that air fills the vacuum between the two helical screws and their housing. The volume decreases as the two screws are rotated, which increases air pressure. Most compressors for rotary screws inject oil into the field of bearing and compression. To minimize internal leakage of this type of air compressor the cooling system, lubrication, and making a seal between the screws and the wall of the building are essentially need to be taking care of. The oil and air have to be separated during the compression period before the air can be used by the pneumatic system.
The other type of air compressor which a rotary screw is positive volume compressors. Its pump has 8 main blades, a stator, and a rotor. Inside the stator, the notched rotor is positioned eccentrically and provides a crescent-shaped sweeping area between 20 gallon for air compressor the intake, and the exhaust outlet. Compression happens as one turn is turned by the rotor when the volume changes from a maximum at the inlet openings to a minimum at the exhaust outlet. The blades, which are pushed out via the slot, are pressed against the stators at high speed. When air is taken in through the inlet, oil is used to cool the air before being pumped through the stator blades in order to reduce the temperature that is generated by the stator blades. The oil and air have to be separated during the compression cycle so that the air can be moved to the pneumatic system.
Rotary vane vs. rotary screw compressors
In terms of operation
A rotary vane compressor consists of a displaced rotor. The blades rub against the cylinder wall and form an airtight seal as the rotor rotates around its axis. Atmospheric air reaches the hermetically sealed and is pressed into it, and then compresses it.
The rotary screw compressor consists of two parallel screw rotors that lock when rotated in the cylinder, one male and one female. The two rotors rotate and intertwine as ambient air enters, trapping air in the space between them and compressing it.
Energy Efficiency
There is limited internal air loss from rotary air compressors, which means that they are more energy-efficient. The blades have the potential to stay in constant contact with the cylinder surface by lubrication so that the tightness of the air is almost perfect. An oil that also helps to cool the air during compression is given by this lubrication.
Rotary screw compressors, sadly, have a “hole” that leads to the loss of internal air and can not be completely removed from the design. Due to the high air pressure returning to the low-pressure region, this “blowing hole” is the position where the outer rotor profiles join.
What’s the best option?
Without knowing what you need from a compressor, it is hard to tell which one will be the best option for you. But after the introduction almost a hundred years ago, the vane theory was more developed. And as per the manufacturer’s specifications, a rotary vane compressor can last up to 100,000 hours without deterioration, even in environments with relative dust.
However, in terms of performance and compatibility, rotary screw compressors deliver a range of advantages. For instance; they’re much better at saving energy. Not only can they produce less heat than traditional air compressors, but they also help to reduce the regular cost of service, resulting in optimum performance.
We would be happy to help if you are not sure which form of tool fits your needs. We have over 10,000 air compressors you can choose from. We also provide impartial and truthful advice to guide your needs. We can easily find the right solution for your particular applications by offering compressed air solutions for over 50 years, helping you to make your processes more energy efficient.
To many people, a vane compressor is better than a screw compressor, and in this section, we will discuss the description of what gives an advantage to a vane compressor over a screw compressor.
Energy Efficiency
Approximately 10% of the energy used in the factory is devoted to the processing of compressed air, so a significant cost-saving measure is the efficient operation of air compressors.
To compensate for the leakage paths inherent in the construction and which deteriorate over time, the rotary screw compressor works at high speed. The nature of the pallet does not have this problem, so it can operate at slower speeds, resulting in increased energy efficiency and lower energy consumption.
For the first thousand hours of usage, the performance of the vane compressor actually increases, while when the bearings wear out, the rotary form becomes less efficient.
Long-term Performance
The rotors in the screw unit predominantly use high-quality steel that can be quickly machined. With edge lubrication, this type of steel tends to wear. At each start-up, metal-to-metal touch triggers this form of wear because the variator does not retain oil.
For the rotor, stator, and end cap, the blade usually uses high-quality cast iron. As it contains oil, the use of this bearing material is significant. As long as the blade that comes into contact with them are made from another metal, compared to one type of screw, the wear is minimized over time.
Without replacing the white metal brushes usually used, most vane compressors operate for over 200,000 hours. Roller bearings should be replaced every 30,000 to 40,000 hours of service.
Easier Maintenance
Like the oil tank, the thermal bypass, and some power regulators, the accessories on both tools are very similar. This implies that there will be fair maintenance work and the expense of these things.
But screw types are more costly and reliable for compressor repairs and often require a shift in the factory. While vane compressor can be serviced at the place of work without moving it to anywhere. Blade replacement, which can take up to several hours, depending on size, is the most common repair form of a vane compressor.